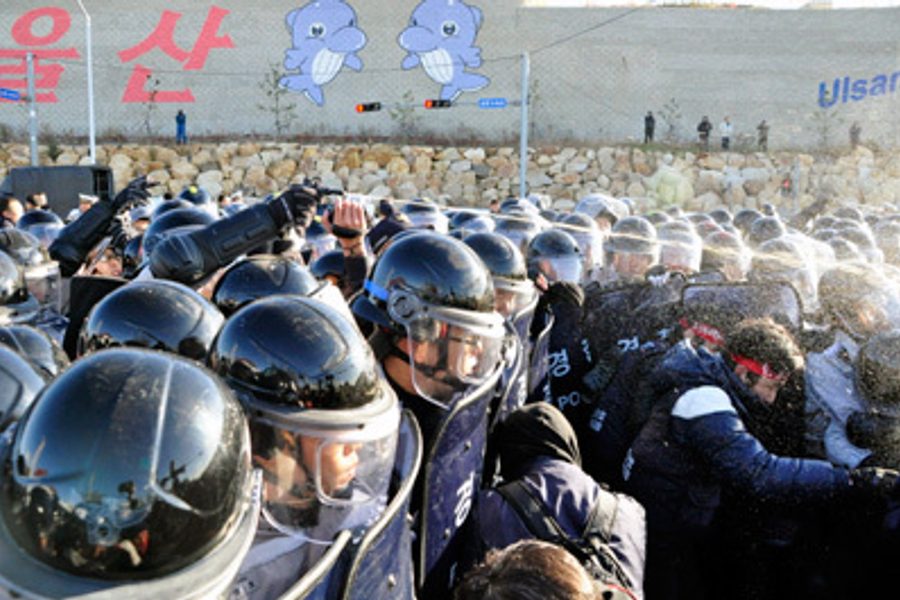
A once-humming Hyundai factory in Ulsan, Korea has become a “cold wintery island” where people are fainting from malnutrition as workers are on their fourth week of a sit-down strike by so-called “irregular” temporary subcontract workers who are demanding permanent positions.
There have been three-way meetings between the company, the union of irregular workers and the union representing full-time workers, though the Korea Times reported the full-time workers’ union has been “reluctant” to support the temps’ struggle. On Wednesday the 45,000-strong union voted whether to support the temporary workers. Later, Yonhap reported that all unions involved agreed to enter negotiations with management together and would suspend strike action at that time.
Such an agreement was originally considered unlikely as the Korea Times noted:
Understandably, the unions would not want others to join their ranks since they are not ready to share the pie promised by management.
Since beginning their strike Nov. 15, the workers have prevented the production of more than 24,000 cars, at a cost of more than $238 million. Management from the Seoul-based company reportedly started some manufacturing even as the strike was going on, with workers disrupting the “half-strength” production.
The Korea Herald reports:
Hyundai had modified the assembly line to allow part of the production process to be carried out manually in order to bypass areas under the control of striking workers ― the automated storage facility, and the conveyor that connects the paint shop to the general assembly section of the line…The non-regular workers had occupied three assembly lines early on in the strike but withdrew from other facilities maintaining control only over the line that produces subcompact cars Accent, Click and Verna.
Recently about 150 members of the UAW union protested outside the Hyundai-Kia America Technical Center in Michigan. A few members of Detroit’s striking symphony orchestra also joined the protest. UAW president Bob King called the effort an example of the union’s stepped-up emphasis on global justice. The move toward employing temporary, subcontracted workers to do the jobs full-time, direct-hire workers had previously done is of course a trend worldwide in many different industries, gutting the well-paying blue-collar union jobs of yore that essentially built the middle class in the U.S. and other countries.
King is traveling to Korea and met with workers Dec. 10. He has raised the possibility of the UAW trying to organize workplaces in other countries, including Korea. Labor leaders worldwide are seeing the Ulsan occupation as an inspiring example of the tactics and determination needed to combat increasing moves by employers in various sectors to resort to subcontractors and temporary workers with few rights or benefits, in jobs that once offered solid union wages.
As the Korea Times says:
Since the nation’s laborers started organizing unions en masse in the late 1980s, companies have realized that they could no longer resort to cheap labor to combat the rise of the unionists. Making substantial concessions to unionized regular workers, they adopted a brand new strategy of employing in-house subcontractors for job openings caused by regular workers leaving. It is a kind of win-win solution both for management and labor ― the former can take advantage of workers who they are allowed to fire at anytime by changing the subcontractors while the latter secured good salaries and other perks. The only losers were irregular workers, who typically do the same job as regular workers for much less.
Kari Lydersen is a Chicago-based journalist, author and assistant professor at Northwestern University, where she leads the investigative specialization at the Medill School of Journalism, Media, Integrated Marketing Communications. Her books include Mayor 1%: Rahm Emanuel and the Rise of Chicago’s 99%.