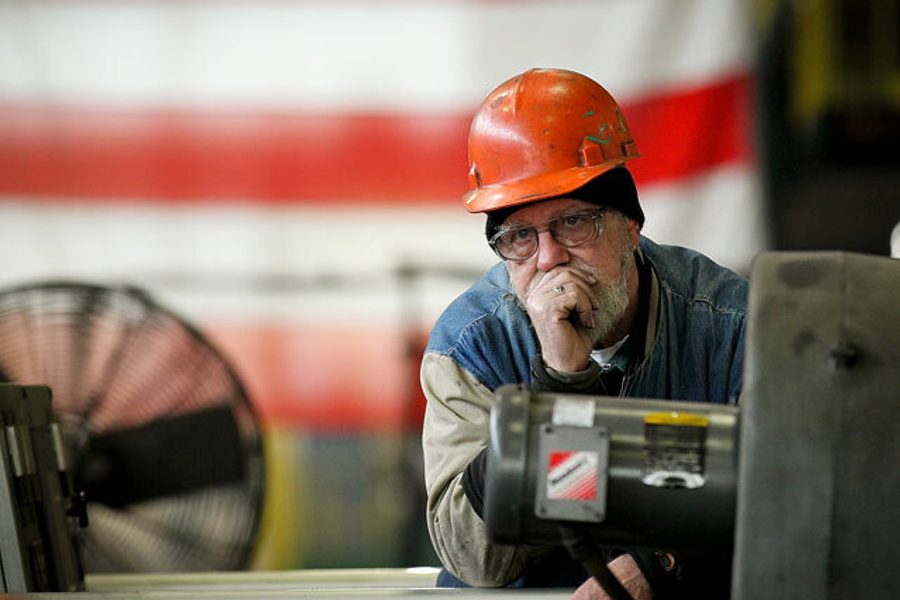
During the last century, most Americans believed their Yankee ingenuity at making things would pave the road to mass prosperity. Then, in recent decades, American innovation switched focus from producing goods to placing wild financial bets, and if U.S. companies made things, they increasingly did it overseas. The result? The wealthiest 1 percent left everyone else eating dust on the side of the road. But now, economic strategists, President Barack Obama and the majority of Americans are reaching the same conclusion: We need to give new life to making things in the United States if we hope to regain a chance at broadly sharing the nation’s once-and-future wealth. In the president’s State of the Union address this year, he declared one of his second-term priorities to be “making America a magnet for new jobs and manufacturing.”
It’s a dream that resonates with the public. A 2012 survey commissioned by the business-labor group Alliance for American Manufacturing found that 67 percent of voters strongly supported a national strategy to revive manufacturing. Both Independents and Democrats surveyed ranked manufacturing as their top economic issue, putting their hopes in a sector that once formed the bedrock of the U.S. “middle class” by providing well-paying blue-collar jobs.
That bedrock shifted in the late 1990s and early 2000s, when American trade agreements, such as the establishment of Permanent Normal Trade Relations with China, opened the way for manufacturers to move production overseas. During the 2000s, the United States lost nearly one-third (roughly 5.7 million) of its factory jobs. Manufacturing employment dropped during the 2001 recession, continued to decline throughout the recovery and plummeted even further during the Great Recession of 2008.
But as the economy slowly recovers, the president and some analysts have highlighted signs of manufacturing returning from overseas to American factories — a trend variously dubbed “reshoring,” “inshoring” or “onshoring.”
Obama has taken every opportunity to hail the tally (now 500,000) of manufacturing jobs that have been created since the depths of the Great Recession in January 2010. Last year, he visited the Master Lock factory in Milwaukee to celebrate the return of 100 jobs from China. He has also lauded Ford for returning work from Mexico, Caterpillar for reshoring from Japan, and Apple for promising to build some Macs in the United States.
The media and analysts have chimed in. In December, The Atlantic published a glowing cover story about General Electric’s decision to reopen part of its Louisville, Ky., “Appliance Park” to manufacture products previously made in foreign factories. In a 2011 report, “Made in America, Again,” the Boston Consulting Group, which provides strategic advice to corporate managers, predicted that reshoring would lead to the creation of hundreds of thousands of manufacturing jobs by 2021, reducing unemployment by as much as 1.5 percent.
But how real is reshoring? And what kind of jobs is it bringing back? If manufacturing revives, what will it look like?
The tides of reshoring
In the short period since American multinationals departed en masse for China, the headwinds facing global manufacturers have changed significantly, says Scott Paul, president of the Alliance for American Manufacturing. China’s once-rock-bottom labor costs have risen as factory wages in coastal areas climb — due in part to a wave of worker insurgency — and the national currency slowly appreciates in value. The drawbacks of manufacturing in China, once overshadowed by low costs, are becoming more obvious: intellectual property theft, poor quality control, delays, the difficulties of both oversight and nimble adaptation from afar, separation of designers and engineers from the shop floor, rising shipping costs, official corruption, and a workforce that turns over rapidly.
Conversely, the United States offers several overlooked advantages. One is an edge in automation, robotics and other productivity tools that reduce direct labor expenses, undercutting the overseas advantage of cheap labor. Another is proximity to corporate headquarters — at least, for U.S. companies — and to the rest of the supply chain.
Hudson Precision Products, a family-owned, metal-machining shop in the Chicago suburb of Broadview that employs 87 workers, provides a study in miniature of the realities of offshoring and reshoring. The shop suffered in the 2000s as many longtime clients left to chase after ostensibly lower prices in China. “It left a bad taste in my mouth,” says Hudson’s president, Jim Wrenn. “A lot of the work we lost we thought we’d never get back.”
Hudson adapted by upgrading its technology so that a fifth of its machines can now churn out parts unattended overnight. And it sought out clients such as medical equipment firms that need guaranteed quality. But it also made a strategic decision, after largely freezing wages during the Great Recession, to offer a profit-sharing plan that rewards the workmanship and efficiency of its non-union shop employees (who are paid from about $10 to nearly $30 an hour). Because so many of its products are specialized and require only short runs, Hudson cannot automate most of its work, but must instead rely on skilled, strongly motivated employees with good morale.
Wrenn now feels partly vindicated as business has begun to trickle back from customers unsatisfied with Chinese manufacturing. Orders are coming in for small parts in valves, regulators and electronic equipment, many machined to tolerances of a few ten-thousandths of an inch.
Yet only 15 to 20 percent of Hudson’s lost work has returned. Some clients are splitting orders between Hudson and Chinese suppliers, while others are using the shop to provide parts to final assembly operations that have moved from China to Mexico — where the factories are closer to U.S. headquarters but labor is cheaper than in the United States.
“It’s getting to be a more level playing field,” Wrenn says. “I guess that could be called reshoring of a sort.”
The broader numbers bear out Wrenn’s caution. Of the roughly 500,000 manufacturing jobs created since the economy bottomed out three years ago, as much as 60 percent can be attributed not to reshoring, but to the governmentled restructuring of the auto industry, according to Economic Policy Institute economist Robert Scott. Harry Moser, a retired machine tool company executive and founder of the Reshoring Initiative, a group that encourages managers to calculate more accurately the full costs of offshoring, figures that since the end of the recession, companies have reshored about 50,000 jobs, accounting for just 10 percent of the manufacturing employment recovery.
Even this modest estimate may fail to factor in the slow bleed of continued offshoring. While Obama praised reshoring at Master Lock in Wisconsin, typically understated federal figures showed that the state lost 2,777 jobs last year to import competition and offshoring (such as the decision by Joerns Healthcare to move its Stevens Point, Wis., operation to Mexico and to U.S. states with laxer labor laws, eliminating nearly 150 Wisconsin jobs). And GE’s decisions over the past few years to close U.S. plants and move production offshore more than offset the much-ballyhooed GE jobs that have returned to the United States, according to calculations by Chris Townsend of the United Electrical Workers.
“I wouldn’t say there’s a huge onslaught of manufacturing returning from offshore,” says Leo W. Gerard, international president of United Steelworkers, the nation’s largest manufacturing union. “It now appears to be more of a constant trickle.”
Two roads to recovery
The other question at hand is the quality of the reshored jobs. Hudson offers an example of a company that’s pursued reshoring through innovation and some collaboration with workers, but most U.S. companies have taken a lower road — one paved with assumptions that manufacturing can recover only if wages are cut, business taxes lowered, regulations gutted, benefits slashed and unions suppressed. As The Economist noted in a January report on reshoring, many of the celebrated examples of new U.S. factories are in states such as Texas, Alabama and North Carolina that have passed “right-to-work” laws, which weaken union power. Wages in these states are, on average, 3 to 10 percent lower than in other states, and workers are less likely to have employer-sponsored healthcare and pensions.
The Boston Consulting Group’s optimistic estimate of hundreds of thousands of reshored jobs depends on this low-road strategy. Its analysis compares costs in Chinese factory centers, like Shenzhen, with U.S. manufacturing costs in right-to-work, low-wage, largely non-union states, like Mississippi.
There is another road. Some countries pay higher manufacturing wages than the United States: $49.12 an hour total compensation in Sweden and $47.38 in Germany in 2011, for example, compared to $35.53 in the United States. More of their workforce belongs to unions. Yet their manufacturing sectors thrive and account for a larger share of their overall economies.
On this high road — followed to varying degrees in Germany, the Scandinavian countries, other high-income continental European nations and Japan — both the countries and their companies tend to treat workers less as costs to be slashed, as in the United States, and more as assets and contributors. Workers reap the benefits of public investments in things like education, transportation, child care and healthcare. The ripple effects — a more egalitarian distribution of income, a stronger domestic market, a better-skilled workforce — strengthen the country’s economy and social fabric.
Not your father’s factory
The high road offers a chance to preserve what was good about American manufacturing in its heyday, but that doesn’t mean manufacturing will ever look just as it once did. Labor-intensive sectors that have shed the most jobs, such as apparel or consumer electronics, are unlikely to revive unless U.S. breakthroughs in automation dramatically reduce the need for direct human labor. With Chinese labor costs rising, multinationals making such goods are simply seeking cheaper labor in countries like Vietnam or Bangladesh.
Instead, the U.S. factories of the future will have to compete with the most advanced manufacturing facilities in the world, whether they are in northern Europe and Japan or in emerging powerhouses like Brazil. That means investing in the kind of manufacturing that relies on skill, capital and advanced research — an approach that can be used to make new products like clean energy technologies, as well as established but evolving products like automobiles.
Should the United States go all-in on this kind of advanced manufacturing, the entire economy stands to gain. Advanced manufacturing creates more non-manufacturing jobs in fields such as research, software design and after-sale support — than traditional manufacturing. And by increasing productivity, it enables (but does not guarantee) higher wages. In fields such as medicine and energy, advanced manufacturing can — if guided by public policy — contribute to solving society’s problems, including the environmental problems caused by earlier phases of the Industrial Revolution. Manufacturing for domestic use and for export can reduce the unsustainable long-term trade deficit. And a healthy advanced manufacturing sector contributes to the creation of a culture of networked innovators — dubbed the “industrial commons” by Harvard Business School professors Gary Pisano and Willy Shih. (Think Silicon Valley, for example.)
What would such advanced factories look like? Well, for one, some of the workers on the line might resemble Baxter: a friendly-looking humanoid robot with a red and black plastic body, a flat-screen face and two expressive eyes that move and emote. A factory worker can easily teach Baxter to do varied jobs simply by guiding his two arms through the motions, then pushing a programming button. Then, Baxter uses his vision to adapt to changes in his work environment.
Baxter is the brainchild of Rodney Brooks, an MIT roboticist who, working with colleagues in 2002, invented Roomba, a robotic household vacuum cleaner. His firm, iRobot, began producing Roomba in China to take advantage of cheap labor, but Brooks concluded that this business strategy was flawed. Costs started going up. The distance between the engineers and Roomba’s production line posed problems, as it was difficult to monitor factories and deal with disruptions in global supply lines. And within months of the factory opening, China’s notorious intellectual property pirates began producing Roomba knock-offs.
To make such a product successfully in the United States, Brooks thought that a business would need cheap, flexible robots to reduce the cost and errors of routine work. So five years ago, Brooks founded Rethink Robotics to design and manufacture Baxter in the Boston area. “The company’s business is to make American manufacturing more competitive and to keep manufacturing from moving overseas,” says Rethink Robotics field engineer Mike Fair.
When many people hear about robots like Baxter, they understandably worry that these increasingly flexible, smart machines will displace humans. Indeed, Fair says that at current prices, Baxter can cost-effectively replace routine workers who are paid $4 an hour or more. But Baxter can’t beat out even lower-paid workers, and he can’t do sophisticated jobs.
The challenge posed by robots such as Baxter is profound: The gains from their increased productivity — whether taken as higher incomes or shorter hours of work — must be shared socially, so that everyone benefits. That may sound utopian, but the alternative — an economy where many people are made redundant because robots are doing the work and only a privileged few benefit — is ominously dystopian.
The hybrid approach
Baxter shows how American manufacturers have already begun to innovate in advanced manufacturing. But he faces competition. At the Automate trade show in January, many of the big exhibitors of factory automation equipment hailed from companies with headquarters in Germany, Japan, Scandinavia, Switzerland and other rich, high-road countries. Near the Rethink Robotics exhibit, a Danish firm — Universal Robots — demonstrated a more abstractly human, elegantly designed flexible robot that appeared to do what Baxter does. In the long run, companies developing new means of production are likely to gain an edge if they are immersed in thriving manufacturing communities nurtured by high-road industrial policies.
The field of automation and robotics is only likely to grow more crowded as China deals with rising labor costs by embracing advanced manufacturing. For example, Foxconn, the Apple product manufacturer — whose working conditions have given rise to suicides, strikes and riots — reportedly plans to leapfrog ahead of manufacturing giants in richer industrialized countries by replacing 1 million workers with robots.
The future success of any country’s firms in advanced manufacturing will have less to do with any one factor, like wage levels, than with a vast complex of factors: support for research and education, social and economic security of the population, a sense of community, worker empowerment and encouragement of innovation.
Susan Helper, Timothy Krueger and Howard Wial at the Brookings Institution have laid out such a plan for the United States, one that takes the high road by way of advanced manufacturing. They have called for public policies that support intense public and private R&D, and improvement in lifelong general and job-specific education, and the collaborative inclusion of workers in decision-making.
The way ahead
Should we look to Obama to take the high road? He showed mettle in his first term, when his administration halted the collapse of the nation’s auto industry and invested more federal resources in renewable energy than under any previous president.
Obama’s initial proposals for the next four years are modest, but good. He has called for basic scientific research funding, including a recent proposal to spend $100 million on mapping the human brain. He advocates using oil and gas revenue from federally owned land for research on alternative auto technology; federally funding energy efficiency in buildings; and expanding infrastructure spending.
Such ideas are unlikely to win much, if any, Republican support. Democrats express various degrees of enthusiasm, often in proportion to their region’s reliance on manufacturing. Business leaders are divided — typically by their own narrow, special interests — and united in hostility to most regulation. And labor unions seek a broader, more ambitious strategy.
Obama can take some actions on his own, like enacting his plan to create 15 “manufacturing innovation institutes.” A pilot institute was started last year in Youngstown, Ohio, to accelerate development of 3-D printing, a promising new technique that uses a machine to deposit layers of different materials, instead of ink, to build easily customizable products.
In his State of the Union address, Obama noted his first-term success in doubling the nation’s wind, solar and geothermal energy capacity, and pledged to expand the effort, which drew harsh criticism from the Right. Republicans waved the bloody shirt of Solyndra, a solar cell maker that received federal loan guarantees but went bankrupt, as proof that government should not get involved in helping fledgling industries. But Solyndra failed in part because of competition from government-subsidized Chinese firms that allegedly dumped their conventional silicon photovoltaic cells at prices below cost to gain market share. With prices plummeting faster than anyone had predicted, Solyndra’s alternative solar technology was unable to compete, and the company went out of business.
On the whole, the federal clean energy loans created jobs and spurred clean energy manufacturing and deployment in a cost-effective manner, according to a review by a commission led by Herb Allison, Sen. John McCain’s former national finance chair. The administration’s track record even beats the performance of many private investors: Approximately 8 percent of companies receiving federal sustainable energy aid in the first Obama term went bankrupt, compared to 22 percent of Bain Capital investments under Mitt Romney.
But ultimately, despite his promises of a manufacturing revival, Obama’s plans fall short of the effort needed. His commission on advanced manufacturing recommended that government should make an economic climate more inviting for manufacturing, but that is typically a recipe for general business tax cuts and deregulation with no strings attached. While taxes should not disadvantage domestic manufacturing or subsidize offshoring, tax incentives — even to invest domestically — are less precisely targeted and less effective than other forms of support.
And considering that offshoring, especially to Asia, has created the current manufacturing crisis, Obama’s goal of extending the current model of free trade agreements to both Europe and the Pacific is at odds with his dreams of a factory renaissance. Meanwhile, his neglect of unions in his State of the Union speech sounds an ominous note for a high-road manufacturing strategy.
The trickle of reshoring has raised public hopes, as well as valid doubts about the infallible wisdom of executives who stampeded offshore with little appreciation of the needs or potential of their workers. But a real renaissance in American manufacturing will require energetic, high-road government intervention with an eye to innovation, not simply fatter paychecks in Guangzhou province.
David Moberg, a former senior editor of In These Times, was on staff with the magazine from when it began publishing in 1976 until his passing in July 2022. Before joining In These Times, he completed his work for a Ph.D. in anthropology at the University of Chicago and worked for Newsweek. He received fellowships from the John D. and Catherine T. MacArthur Foundation and the Nation Institute for research on the new global economy.